Has this ever happened in your workplace?
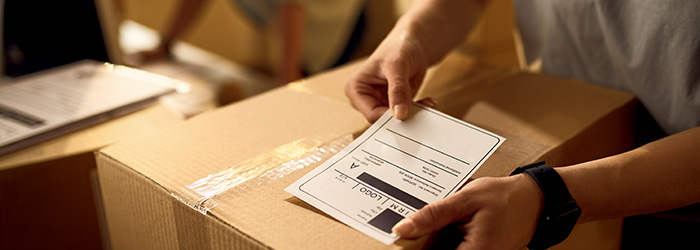

- Product codes for overseas markets are different from those for domestic markets. Because products destined for overseas markets do not have barcodes, binning inspection is limited to a simple visual check, leading to frequent shipping errors.
- Products are not properly sorted at binning, and consequently end up being mixed together on pallets and then shipped out incorrectly.
Solution

- Where different product codes are used for domestic and overseas markets, overseas product labels should be generated during binning inspection at the overseas warehouse. This will boost the accuracy of subsequent warehouse operations (i.e. reduce shipping errors) and may even reduce workloads as well.
- POINT
Labeling products at binning ensures they are sorted correctly and enables better inspection prior to shipment. Also, by utilizing binning labels and adding not only the item but also the lot, quantity, production date, and expiration date to the unit of issue, it is possible to prevent product mix-ups from an even more detailed perspective.
Overseas products labeled at binning inspection
Has this ever happened in your workplace?
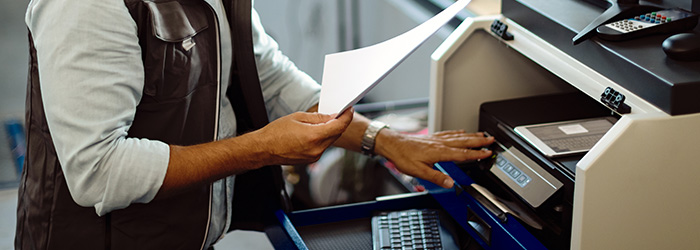

- Workers at overseas warehouses are rotated frequently, leading to incorrect shipment quantities being entered on picking lists, and incorrect quantities being shipped.
Solution

- Shipping instructions are loaded directly into the system, which automatically generates picking lists and shipping dockets. This eliminates manual data entry and therefore helps to reduce human error.
- POINT
Human error in data entry is inevitable if data is not properly linked between systems — for instance, where picking lists are generated in Excel and data for shipping dockets is manually entered on screen.
The key is to set out rules and processes designed to minimize the manual input component, as well as checking procedures designed to identify simple errors before they result in incorrect shipments.
Issuing picking instructions and work forms are based on shipment instructions
Has this ever happened in your workplace?
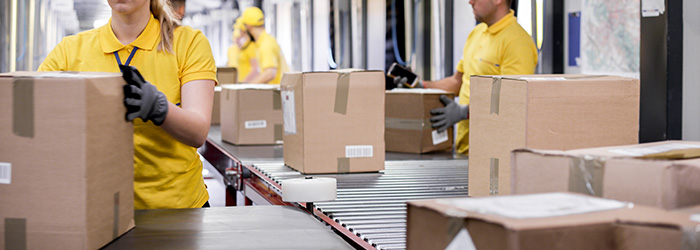

- At overseas distribution centers, workers are often rotated, and the lack of consistency leads to issues such as product labels with incorrect recipient locations, resulting in shipping errors.
- Products are not taken from the correct location specified on the picking list. Failure to detect the error results in a shipping error.
Solution

- The system prints out work forms and shipping dockets before outbound work commences, in order to prevent human error. Another way to eliminate products transfer errors is to forward receiving client details (linked to work forms) to the carrier as part of the shipping inspection.
- POINT
A barcode system for shelves and inventory stock helps to minimize human error. Handheld terminals are used to register locations and stock barcodes which are matched to the work form when picking. This helps to prevent picking errors.
Picking with handheld terminal by scanning shelves and articles
Has this ever happened in your workplace?
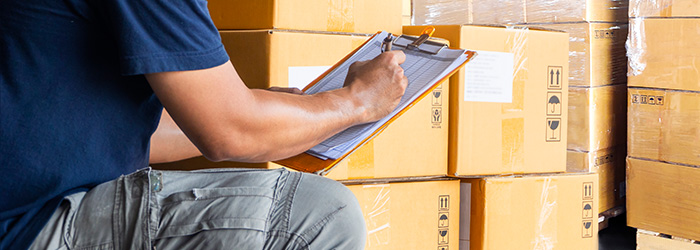

- Products loaded onto wrong truck and sent for delivery.
- Products not loaded onto truck.
- Cases were sorted correctly but worker is diverted to another task and fails to notice that cases have been moved to the wrong location and then shipped.
Solution

- Inspections using handheld terminals during shipping processes (picking, packing, and loading) helps to prevent transporting and loading errors.
- POINT
By monitoring the status of each process, the system can detect picking and loading errors and prevent incorrect shipments.
Loading inspection with barcodes
Contents